The Ultimate Guide to Ultrasonic Cleaning
Ultrasonic cleaning is a process that uses high-frequency sound waves to agitate a liquid, producing microscopic bubbles that, when they collapse, create a high-energy environment that is very effective at cleaning surfaces. This method is used extensively in the cleaning of precision components in a wide range of industries, including medical, aerospace, and automotive.
Ultrasonic cleaning involves the use of high-frequency sound waves, typically between 20 kHz and 100 kHz, to agitate a liquid, usually water or a water-based cleaning solution. The sound waves create microscopic bubbles, or cavities, in the liquid. As these bubbles move through the liquid, they create a high-energy environment that is very effective at removing dirt, grease, and other contaminants from surfaces.
This process, known as cavitation, occurs when the pressure in the liquid drops below the vapor pressure, causing the formation and subsequent collapse of bubbles. When these bubbles collapse, they release energy in the form of heat and pressure waves that dislodge contaminants from the surface being cleaned.
Benefits of Ultrasonic Cleaning
Ultrasonic cleaning offers several advantages over traditional cleaning methods. Firstly, it is very effective at removing contaminants from hard-to-reach areas, such as crevices, blind holes, and threads. Secondly, it is gentle and non-abrasive, making it ideal for cleaning delicate components without damaging them. Finally, it is very efficient, reducing the time and labor required for cleaning.
Limitations of Ultrasonic Cleaning
While ultrasonic cleaning is very effective at removing most types of contaminants, there are some limitations to the process. Firstly, it is not suitable for cleaning very soft metals, such as pure aluminum or thin, soft metals, as the ultrasonic action of cavitation can dent or erode these materials. Secondly, ultrasonic cleaning is not effective for removing heavy deposits of grease or other contaminants that require a pre-wash before ultrasonic cleaning.
Best Practices for Ultrasonic Cleaning
To achieve optimal results with ultrasonic cleaning, it is important to follow some best practices. Firstly, ensure that the cleaning solution is properly formulated for the materials being cleaned and the type of contaminants being removed. Secondly, ensure that the cleaning bath is properly agitated to distribute the cleaning solution evenly and promote cavitation. Finally, ensure that the components being cleaned are properly positioned in the bath to ensure that all surfaces are exposed to the cleaning solution.
Ultrasonic cleaning is based on 3 parameters:
THE MECHANICAL EFFECT:
How will ultrasonic waves help clean the parts?
THE CHEMICAL EFFECT:
Why is it important to use detergents?
Why can’t we clean only with water?
THE QUALITY OF WATER:
How to choose the best water quality?
How to control all of these parameters?
PROCESS CONTROL:
Check all parameters and get perfect cleaning
TIPS TO IMPROVE CLEANING EFFICIENCY:
What can you change?
Ultrasonic Cleaning: Understanding the Mechanical Effect
How are ultrasonic waves produced?
Cavitation occurs due to the stretch and compress phases of the sound waves within the fluid. The bubbles generated during the process implode under the mechanical action of ultrasonic waves, releasing a large amount of energy and causing the local temperature to increase. This energy is powerful enough to force bubbles into crevices, allowing the cleaning fluid to penetrate between the contamination and the workpiece, leaving it clean and free of hidden soils.
The frequency of the ultrasonic waves plays a crucial role in determining the effectiveness of the cleaning process. The most common frequencies used in industrial cleaning applications are 25 kHz, 40 kHz, 80 kHz, 120 kHz, and Megasonic frequencies. Each of these frequencies has unique properties that make them suitable for different cleaning applications.
The 25 kHz frequency is the most powerful and is used for removing strong pollution. However, it is not recommended for sensitive materials like glass, aluminum, and mirror-polished surfaces. The 40 kHz frequency is a standard frequency that is compatible with a wide range of materials and is effective in removing a lot of pollution.
The 80 kHz frequency is used for cleaning parts with complex geometry. The cavitation bubbles generated at this frequency are small enough to penetrate small holes, removing contamination from hard-to-reach areas. The 120 kHz and Megasonic frequencies are mainly used in precision optics to clean very sensitive parts like wafers. The power of cavitation is low at these frequencies, making them ideal for cleaning clean parts to remove dust in final cleaning.
Several factors influence the cavitation process, including the external pressure, temperature, ultrasound frequency, and power, and the nature of the chemicals used to clean, their concentration, and their density. Heated cleaning liquids reduce cleaning time and remove dirt faster, making them a popular choice in industrial cleaning applications.
Importance of Properly Positioning Parts in the Working Chamber
The effectiveness of water-based cleaning processes depends on the close contact between the cleaning chemistry and surface impurities, which is often overlooked when working with parts with complex geometries. Proper positioning of parts in an ultrasonic cleaner is crucial to ensure optimal cleaning performance. When parts are positioned correctly, several benefits can be observed, including improved ultrasonic efficiency through dipping or pressure jet spraying, protection from mechanical damage to the surface, enhanced contact between the substrate and cleaning chemicals, improved efficiency during the rinsing process, and better results during the drying step.
Properties of the Water Molecule and its Chemical Effects
The nature of the water molecule
Water is composed of hydrogen and oxygen atoms, and it exhibits polarity, which enables it to dissolve salts. However, due to its polar nature, water is not miscible with non-polar hydrocarbons such as oils and fats.
Surface tension of water
When a paper clip floats on the surface of water, it experiences an upward force that counterbalances its weight. This force is due to the intramolecular attraction (Van der Waals force) caused by the polarity of the water molecule. Within the liquid, the Van der Waals forces offset each other. At the surface, these forces act inward, causing the liquid to contract and behave like a stretched membrane.
Lotus effect
Water maintains its spherical shape due to its high surface tension.
Corrosion effect - Iron Oxidation
When metallic iron dissolves in water, it undergoes electron transfer, causing it to corrode. Dissolved oxygen reacts with water molecules and electrons to produce hydroxide ions. These ions then combine with iron ions to form iron hydroxide, which can take on various chemical forms as oxide or hydroxide salts.
Why do we need to use detergents to clean parts?
Detergents help to decrease the surface tension of water, allowing it to wet and solubilize oil and fat compounds. They also provide protection against corrosion by incorporating corrosion inhibitors.
Steel wool 30 min in water
HOW DETERGENTS WORK - Understanding the Chemical Process
GREASE REMOVAL - Properties of Oil and Fat
When fats derived from plants or animals are mixed with a caustic solution, a process called saponification occurs. Triglyceride, which is not soluble in water, is broken down into carboxylate ion and glycerol, both of which are water-soluble. It is important to note that certain surfaces, such as copper alloys, may be sensitive to strong alkaline solutions and may tarnish. Fats that originate from minerals cannot undergo saponification chemically, and thus require the use of surfactants.
A surfactant is a substance that possesses a hydrophobic tail and a hydrophilic head. The length of the hydrophobic tail and the composition of the head determine the surfactant's ability to create micelles, which are necessary for effective cleaning.
How do surfactants work?
The Critical Micelle Concentration (CMC) is the minimum concentration at which surfactant molecules begin to form micelles. Without micelles, detergents cannot clean effectively. Below the CMC, the molecules form monomolecular layers. Above the CMC, they form micelles. As more surfactants are added, more micelles are formed. Surface tension does not decrease as surfactant concentration increases.
REDUCING WATER SURFACE TENSION: Surfactants position themselves between water molecules, disrupting their bonding and lowering their force. Some surfactants can decrease surface tension to as low as 30 mN/m.
EMULSIFYING OILS: When oil is mixed with water containing surfactant, the surfactant envelops the oil droplets, with its head attracted to the water molecules and its tail capturing the oil.
Disperse oils into the liquid: To disperse oils into a liquid, surfactants attach to soil or oil droplets by adsorption. The hydrophilic group of the surfactant is in contact with the aqueous phase, while the hydrophobic group is in contact with the oil or soil. The stabilization of the droplets prevents coalescence with other droplets through repulsive forces between the head groups. This specific effect also provides corrosion inhibition by creating a monomolecular film on a solid surface, protecting against oxidation through the hydrophobic effect.
Surfactants fall into four categories: anionic for wettability, cationic for antistatic and antibacterial properties, amphoteric which can be either anionic or cationic depending on the pH of the solution, and nonionic for emulsifying effects. These surfactants have a global mechanism that reduces the surface tension of water, emulsifies pollution, disperses pollution, and protects against corrosion.
A typical detergent is composed of surfactants, sequestering agents for inhibiting negative effects from calcium and magnesium salts, solvents, pH adjustment additives, anti-corrosive additives, specific additives such as preservatives, biocides, anti-static agents, thickeners, and fillers. Three parameters determine the properties of the detergent: compatibility with the substrate and its pH value and composition, efficiency on specific pollution, and the surface treatment of the substrate after cleaning.
Metallic substrates
Metal | Behaviors | Observations | |
---|---|---|---|
Alkaline medium | Acidic medium | ||
Stainless Steel | Resistant excepted in presence of chlorides | Resistant excepted to chlorhydric acid and chlorides | Nitric acid and phosphoric acid will create a passivation layer onto the material. Chlorides will pickle the protective layer. |
Casting iron | Resistant | Sensitive to corrosion | Phosphoric acid will create a passivation layer. |
Copper-Brass-Bronze | Corrosion by coloration change | Sensitive to corrosion | Strong etching with nitric acid. More or less sensitive to ammonium salts |
Aluminum-Zinc and alloys | Sensitive to corrosion | Resistant | White corrosion and tarnish effect can appear |
Nickel | Resistant | ||
Chrome | Resistant | ||
Titanium alloys | Stains can appear | Acidic medium are used as passivation agent | |
Gold | Resistant | Resistant |
Non metallic substrates
Non-metallic substrates can be classified into various types based on their composition and sensitivity to different chemical compounds. In this context, sensitivity refers to the material's vulnerability to damage caused by exposure to specific chemical substances. Ceramics are one type of non-metallic substrate that exhibits sensitivity based on its composition and surface state. The extent of sensitivity varies depending on the specific material. Mineral glasses used in ophthalmic optics and sapphires are resistant to chemical compounds, making them ideal for use in applications where chemical resistance is critical. On the other hand, mineral glasses used in precision optics are sensitive to alkaline, acidic products, and phosphates. Therefore, they need to be handled with care to avoid damage. Organic lenses such as CR39, PA, and High index lenses used in ophthalmic optics exhibit low sensitivity to chemical compounds. However, polycarbonate lenses are sensitive to alkaline products and specific solvents.
It is essential to take into account sensitivity to the corrosion effect due to the pH and the conductivity of water, as well as sequestering agents that can solubilize some elements of materials and create holes. For instance, tungsten carbides bonded with cobalt can be susceptible to damage. The cobalt can be quickly leached by an aqueous cleaning solution, leading to a negative impact on the material's mechanical properties. Carbide grains are included in a cobalt matrix, and any damage to the cobalt can be detrimental to the material's overall performance.
The pollution
The pollution in manufacturing processes can come in different forms, including polishing compounds, oils and emulsions, protection lacquers, oxidation residues, tumbling residues, and even fingerprints.
Polishing compounds are used to grind and polish mineral content, and they can be made from animal and vegetal fats. Oils and emulsions are also commonly used in manufacturing processes, with mineral and vegetal oils being popular choices. Water-based emulsions are also used as lubricants and coolants in various manufacturing processes. Protection lacquers are organic layers that provide mechanical protection during manufacturing processes. They can help prevent scratches, dents, and other forms of damage to the product being manufactured. Oxidation residues can occur on copper alloys or sensitive steel during manufacturing processes or storage. These residues can be harmful to the quality and durability of the product being manufactured. Tumbling residues are often left behind after mechano-chemical polishing with abrasive stones in a tumbler. These residues can affect the surface finishing of the product being manufactured. Fingerprints can also be a form of pollution in manufacturing processes. They can occur after the latest step of the manufacturing process and before controlling. It is important to remove fingerprints to ensure the quality and appearance of the final product.
Surface treatment of substrate
Surface treatment of substrate is a crucial step in many industrial processes. After cleaning the substrate, the surface must be treated to achieve a desired level of hydrophilicity or hydrophobicity. The level of wettability of the surface can be determined by measuring the contact angle of a droplet on the substrate. If the contact angle is greater than 90°, the surface is considered non-wetting. On the other hand, if the contact angle is less than 90°, the surface is considered partially wetting. Therefore, controlling the surface properties of a substrate through surface treatment is important for ensuring proper adhesion and performance in various applications.
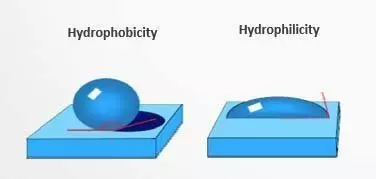
To obtain a particle-free surface during the final cleaning, it is necessary to have a surface that is hydrophilic. This type of surface is also useful for promoting adhesion of coatings with polar or hydrophilic behavior and for facilitating the rinsing process. On the other hand, a hydrophobic surface is necessary for providing corrosion protection, achieving an antistatic behavior, promoting adhesion of coatings with non-polar or hydrophobic behavior, and facilitating the drying process.
View our full range of ultrasonic cleaning fluids here
Rinsing Stages and the Influence of Water Quality
Water quality is an important factor that influences the effectiveness of cleaning processes. A key aspect of cleaning involves the rinsing stage, which helps to remove residues and contaminants left behind after the cleaning process. Different types of water are used for rinsing depending on their chemical composition and quality.
Water qualities
TAP WATER
Tap water is commonly used as the first rinsing step in the cleaning process. However, its quality can be quite heterogeneous, depending on its source. Tap water can have high conductivity of up to 600-700 microSiemens per centimeter and high levels of calcium and magnesium salts, which can leave salt residues on the cleaned parts. It may also be contaminated with organic and chlorine materials. Tap water is best used for cleaning applications where a homogeneous water quality is not essential, and no critical surface quality is required.
SOFTENED TAP WATER
Softened tap water can be used as the first rinsing step when the tap water has a very high content of calcium and magnesium. The quality and conductivity of softened tap water are similar to that of tap water, but the calcium and magnesium ions are replaced by sodium ions through ion exchange. This helps to inhibit low-soluble salt deposition. Softened tap water may, however, be contaminated with bacteria.
OSMOSIS WATER
Osmosis water is used for the preparation of cleaning solutions when the tap water has a very high calcium and magnesium content. Osmosis water is produced by low porosity membrane filtration, which retains up to 90% of the salt content. Osmosis water has a conductivity of 10-20 microSiemens per centimeter and helps to eliminate most organic and bacterial contamination.
DEMINERALIZED WATER
Demineralized water is the final rinsing step before drying, and it helps to eliminate all residual salts. Demineralized water is produced and recycled through ion exchangers, specifically mixed bed resins. The salt content of demineralized water is very low, with a conductivity of less than 0.1 microSiemens per centimeter. However, it may be contaminated with organics and bacteria and requires complementary treatment with UV and active charcoal.
Ion exchange is a process used to remove dissolved ions from water. It involves the use of solid materials, which are chemically grafted with ionic functions that can fix ionic species such as dissolved salts. Cationic ions exchangers retain cations like Na+, while anionic ions exchangers retain anions like Cl-. A mixture of cationic and anionic ions exchangers is a mixed bed.
The Influence of Water Quality on Microbiology - A Critical Parameter Often Overlooked
Bacteria and algae can thrive in aqueous environments with temperatures ranging from 20°C to 40°C. They can be found in both the demineralized water plant and the rinsing tank, and if the tank walls are slippery, it's a clear indication of bacterial growth. It's important to note that bacteria and algae can also contaminate cleaning solutions when used at low temperatures and a neutral pH value.
PROCESS CONTROL - Cleaning solution
When air bubbles are present in a liquid, their internal attractive forces cause them to compress. As a result, the pressure within the bubble increases as its radius decreases. This principle is utilized in the bubble pressure method, which measures the pressure within a gas bubble immersed in a liquid.
To conduct the measurement, a gas stream is pumped into a capillary immersed in the fluid. The bubble that forms at the tip of the capillary continually increases in surface area while its radius decreases until it reaches its smallest size, forming a hemisphere. At this point, the pressure within the bubble reaches its maximum level, and a characteristic pressure pattern develops as the bubble quickly increases in size and eventually bursts away from the capillary, allowing a new bubble to form.
By analyzing this pressure pattern, the surface tension of the liquid can be determined. The bubble pressure method is a valuable tool for controlling the cleaning process and ensuring that the cleaning solution has the desired surface tension for optimal performance.
Cleaning Test Equipment: Importance and Techniques
The quality of the products we use and consume depends on the cleanliness of the equipment used to make and package them. Therefore, maintaining clean equipment is essential for ensuring product quality and safety. To achieve this, a variety of cleaning test equipment is used, each designed for specific purposes.
Refraction Index Measurement
The refractive index measurement is used to determine the concentration of a compound in a sample based on the principle of total reflection of an incident beam at the boundary of the sample and the glass prisms. This requires that the sample has a lower refractive index than the prism, so prisms are made of high-index glass. To establish the standard curve of the refraction index as a function of concentration, the temperature must be fixed. The refraction index will be a function of both concentration and temperature for a single compound.
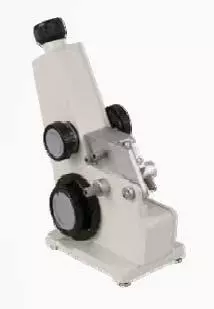
UPC 3000 (Ultrasonic Process Controller)
The UPC 3000 is an ultrasonic process controller that monitors the key parameters of a cleaning process to ensure its quality. The device measures temperature and conductivity directly and monitors ultrasonic power variations in the baths. In addition, the UPC 3000 ensures quality control of DI-Water in the final rinsing tanks and can be configured to meet the customer's specific needs. The device is controlled through a simple menu and three keys, making it easy to use.
AQUASNAP
The AQUASNAP system is used to measure ATP in bacteria, as each bacterium is composed of a fixed amount of ATP. The liquid and reagents are mixed in a snap, and the ATP binds to a reagent that emits light (luciferase/luciferin). The device then measures the amount of light emitted, which is expressed in Relative Light Units. The amount of ATP is back-calculated, allowing for the amount of bacteria to be deduced. The AQUASNAP system is widely used in the food industry to monitor the cleanliness of surfaces and equipment.
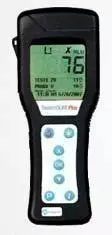
Dyne test pens
Dyne test pens are used to determine the surface tension of a material by applying marking inks to the surface. This method is particularly useful for operators on production lines as a routine check. The result can be immediately evaluated and provides a clear picture of the degree of treatment or cleaning required by trained staff. The marking inks show that the surface tension of the surface is at least 30-32 mN/m. This information is important for ensuring that surfaces are clean and free of contaminants.
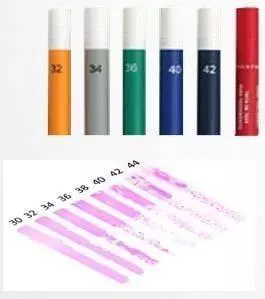
Contact angles measurements
To determine the surface energy of a material, the contact angle between the surface and a liquid drop is measured. This can be done using a picture of the drop shape over the material being characterized. If the liquid used is water, a big angle means the surface is hydrophobic, while a small angle means the surface is hydrophilic. This method is particularly useful for evaluating the cleanliness of surfaces and equipment used in the food industry, as hydrophobic surfaces can harbor bacteria and other contaminants.
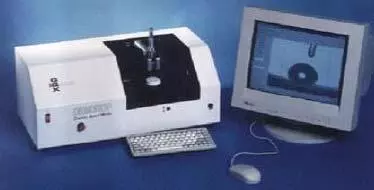
Tips to improve cleaning efficiency
Stabilize your water quality
The aqueous process, which uses water as a cleaning agent, is a popular cleaning method in many industries. Water can represent up to 95% of the cleaning solution, making it a cost-effective and environmentally friendly option. To improve the efficiency of the aqueous process, it is essential to stabilize the water quality. Filtration cartridges can be used to filter out particles with a porosity between 5µm and 20µm, resulting in a good rinsing effect. However, dissolved salt is not filtered out by filtration cartridges, and the conductivity before and after filtration remains similar. Bacteria and chlorine are also not retained.
Softening Device
A softening device can be used to improve the quality of water in the cleaning solution by removing dissolved salt. This device retains dissolved salt, resulting in a similar conductivity before and after filtration. However, the rinsing effect is reduced because Ca2+ and Mg2+ ions are replaced by Na+ ions. Bacteria and chlorine are also not retained.
Mix of technologies
A mix of technologies can also be used to improve cleaning efficiency. This combination of technologies retains particles in suspension, with the porosity to be adapted, resulting in a good rinsing effect. Bacteria and chlorine are also retained.
Filtration cartridge + Softening + Nano-filtration necessary:
To achieve the highest cleaning efficiency, a combination of filtration cartridges, softening devices, and nano-filtration is necessary. This combination stabilizes the cleaning process, resulting in stable processes and constant lens surface quality.
Stabilize your process
To ensure a constant lens surface quality, several key parameters must be controlled.
- The concentration of active tanks must be controlled to ensure stable processes. The concentration can be controlled by monitoring and adjusting the frequency and refresh of the tanks.
- Efficient transducers and sufficient ultrasonic power are necessary to ensure optimal cleaning efficiency. Transducers and ultrasonic power should be regularly checked for defects.
- The conductivity value in each active tank should be in compliance with the supplier's specifications. Conductivity can be used to monitor pollution levels in the cleaning solution.
- The conductivity value in the DI-water tank should match the measurement of the DI-unit. The quality of DI-water should also be regularly checked.
Improving cleaning efficiency is essential to ensure product quality, process stability, and plant profitability. The use of aqueous processes, filtration cartridges, softening devices, a mix of technologies, and a combination of filtration cartridges, softening devices, and nano-filtration can all contribute to improving cleaning efficiency. It is also crucial to control key parameters such as the concentration of active tanks, ultrasonic power, and conductivity values to ensure stable processes and constant lens surface quality.